Connected Worker RTLS
Litum's real-time location system for connected workers is designed to deliver tangible results across diverse environments, including warehouses, factories, offices, and hospitals. Backed by our proven expertise, organizations can streamline workflows, enhance employee safety, and ensure rapid response in critical situations, driving both efficiency and well-being.
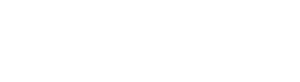
The Smart Way to Keep Workforce Safe and Operations Efficient
At Litum, we understand that keeping your workforce safe and operations running smoothly is a top priority. Our connected worker solution is designed to provide real-time visibility into employee locations, helping you respond quickly to emergencies, improve workflow efficiency, and ensure compliance with workplace safety standards.
Many of our clients have seen tangible benefits, like reduced downtime, better resource allocation, and a safer working environment. With accurate data at your fingertips, you can make informed decisions that not only protect your employees but also contribute to measurable savings for your business. This isn’t just about technology — it’s about creating a workplace where safety and productivity go hand in hand.
*Covered by Litum solutions to date
Where Safety Meets Productivity
Real-time location data and reports to optimize workforce operations
Real-Time Location Data
- Strengthen emergency response with precise location awareness, ensuring employees are quickly located and assisted during crises
- Optimize workflows by identifying and addressing bottlenecks, enabling employees to complete tasks more efficiently
- Enhance safety with real-time alerts for access to restricted or hazardous areas, reducing potential risks
- Improve facility layouts by analyzing movement patterns, uncovering inefficient zones and traffic congestion points
- Automate compliance and reporting for attendance, safety zone adherence, and time spent in critical areas, ensuring accountability
Zone Occupancy Reports
- Visualize zone occupancy to identify underutilized areas and enhance resource allocation for better efficiency
- Streamline workflows by balancing workloads across zones, reducing bottlenecks, and improving task execution
- Pinpoint high-traffic areas to minimize congestion, prevent delays, and boost overall productivity
- Highlight occupancy trends to optimize space utilization, ensuring even task distribution and smoother operations
- Support data-driven decisions with clear insights into movement patterns and zone usage for measurable improvements
Heat Maps
- Identify high-traffic areas to enhance safety and reduce overcrowding risks
- Highlight zones of prolonged activity, uncovering potential delays or workflow inefficiencies
- Spot underused areas to optimize layouts and improve workspace utilization
- Analyze movement density patterns to balance workloads and ensure even task distribution
- Gain insights into workflow dynamics for continuous improvement and better planning
- Support data-driven decisions by providing clear insights into employee activity and movement trends over time
How Connected Worker RTLS Works
Litum employs advanced ultra-wideband (UWB) and bluetooth low energy (BLE) technology within wireless, rechargeable employee tags, available in badge or compact designs. These devices integrate seamlessly with Litum’s RTLS mesh network, a robust framework that ensures reliable, real-time data transmission across large areas. The mesh network enhances system resilience and scalability, enabling precise location insights even in complex environments.
Our indoor location technology captures accurate movement and positioning data, feeding it into Litum’s RTLS software for complete operational visibility. This empowers organizations to monitor activities in real time and generate detailed reports and analytics, driving smarter, data-backed decisions.
The system also includes powerful features like geofencing, allowing organizations to define virtual boundaries, restrict access to sensitive areas, and automate alerts for policy violations or emergencies. Together, these technologies create a dynamic, efficient, and highly secure solution.
Hybrid Technology for Precision and Efficiency
Combines BLE for less energy consumption and location insights in lower-accuracy environments with UWB for sub-meter precision in critical areas, ensuring optimal performance across diverse facility needs.
Real-Time Insights for Safer Workplaces
Provides instant location insights and safety alerts, enabling faster responses to emergencies and ensuring compliance with safety protocols across the organization.
Actionable Analytics for Smarter Workforce Management
Delivers detailed reports on movement patterns, zone utilization, and task durations, helping organizations optimize workflows, reduce downtime, and improve overall efficiency.
Built for Results, Trusted by Leaders
In-House Expertise, Industry-Leading Results
At Litum, every component — from hardware to software — is designed, manufactured, and rigorously tested in-house. This end-to-end control guarantees seamless performance, faster customization, and innovation at every step. By eliminating third-party dependencies, we provide unmatched quality and agility in adapting to client needs.
Access Dashboards Customized for Your KPIs
Litum’s solutions go beyond real-time insights by delivering robust historical data reporting. Our platforms allow businesses to identify trends, pinpoint inefficiencies, and make data-driven decisions to optimize safety and productivity.
With powerful tools like heatmaps, spaghetti diagrams, and transaction logs, businesses gain invaluable insights into their operations from every angle. Most importantly, our customizable reporting ensures the data is tailored to your unique needs, helping you achieve your KPIs with precision and confidence.
Solutions That Fit Seamlessly Into Your Operations
Litum solutions are purpose-built to integrate with existing industrial systems, including fleet management platforms, maintenance systems, and operational monitoring tools. Our technology ensures minimal disruption while delivering maximum compatibility, enabling businesses to enhance safety and efficiency without overhauling their infrastructure. This adaptability streamlines implementation, empowering organizations to achieve operational excellence with ease.
Certified for Safety, Reliability, and Performance Worldwide
All Litum hardware meets rigorous global standards for safety, durability, and performance. Certified for industrial environments, our devices comply with FCC, CE, and IC standards, ensuring reliability in diverse and demanding settings.
Explore Our Resources
Proven Innovation, Recognized Globally
Explore Our Resources
Discover Litum’s
Unique Edge
Solutions
Shaped by two decades of experience in over 50 countries, reflecting global best practices and diverse on-site experiences
Systems
Built for easy integration and high precision, our system helps companies surpass their safety and productivity goals
Technology
Trusted by some of the world’s most prominent firms, including Fortune 500 companies
Know-How
Two decades of innovation recognized by institutions like Fast Company, Deloitte and Gartner
Global Support
Continuous improvement and dedicated support that adapts to the evolving demands of industries, no matter where you are
Precise Location
Full RTLS deployments that offer high accuracy in location tracking, crucial for dynamic and complex industrial settings