Process Tracking
Identify and track each product on the floor. Control every facet of the production in real time using the process tracking system powered by Litum RTLS
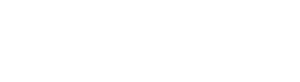
Track each step with Manufacturing Process Tracking
Track and trace manufacturing processes from start to end with our process tracking system. Track products through all manufacturing steps, create alerts for products that fail tests, and trace products through rework. Recognize each product and display specific instructions for the operator, thereby eliminating manual scans. Manage rejects and products through rework.
Track with maintenance status
Maintenance tracking lets you monitor status, calibration schedules, and repair records. Litum process tracking system Instantly identifies assets that require immediate attention, as they pass their due date, with their periodic maintenance or calibration.
Instant notification of breakdowns with maintenance tracking system
Trigger maintenance requests via the call button on the tag in case equipment malfunctions, instead of calling for a maintenance operator. Our manufacturing process tracking software can detect operating malfunctions to enable quick response for repairs.
Improve manufacturing workflows
Provide product-based information to assembly workers and keep production uninterrupted. Record data unique to each product, and gather information that enables analysis of how the assembly system operates and how it can be modified to enhance KPI’s.
Improve repair time with Maintenance Tracking
Track and manage maintenance teams, monitor repair time, and enforce maintenance KPIs (such as MTTR – mean time to repair, MTBF – mean time between failures, etc. using the Litum process tracking system.
Equipment replacement
When a device is down, the manufacturing tracking system can automatically identify, locate, and source a replacement from another department.
Visibility
Production line disruption is prevented by providing visibility into the quantity and location of all raw materials, subassemblies, and finished products
Flexible
The process tracking system facilitates production customization and manufacturing of multiple work orders at a time
Traceability
Critical components of every single product can be identified for traceability using our manufacturing part tracking system
How Maintenance & Process Tracking Works
Litum integrates UHF RFID and ultra-wideband – UWB RTLS technology into battery-powered active RFID trackers installed on the products in the manufacturing process. Litum also provides housings for products to ensure a secure and reliable fit. Our tags work in conjunction with our RTLS mesh network, installed throughout your facility to create an invisible “indoor tracking system” that monitors every product’s location with the highest accuracy available.
Our track-and-trace manufacturing solution and process tracking system can identify malfunctions in assembly processes. The signals from process tracking RTLS tags are converted into location data using various proprietary algorithms. The location of each product is then sent on to our process management software, where it is interpreted and displayed in an easy-to-understand manner, and company-specific business rules are applied. The received data can then be used to monitor the manufacturing process for future improvements and facilitate automated maintenance tracking to reduce downtimes and keep optimal operation status.
Simeco/TEKA streamlined workflows and reduced human error for its kitchen appliances line by Litum’s custom process tracking system, powered by RFID technology.
Find out how.